Crushing machines for forage harvesters
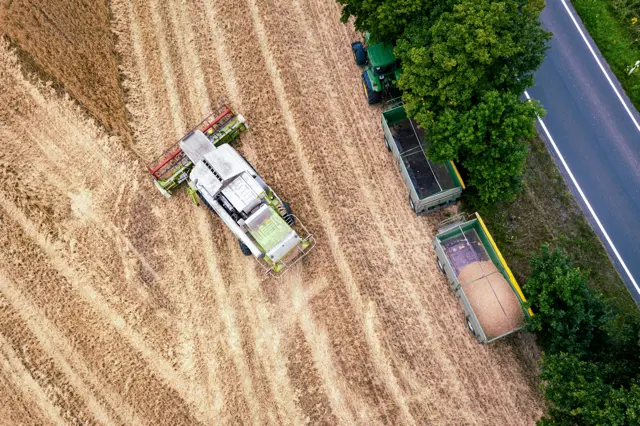
With the development of agriculture, there was a need to replace traditionally used hand tools with more efficient and faster mechanical devices. One of them, increasingly used on farms, is a self-propelled forage harvester with its drive system.
Self-propelled forage harvester – what is it?
A self-propelled forage harvester is a complex, multi-functional agricultural machine that combines many processes in one technological sequence: mowing, collecting plant matter, grinding, pressing, shredding, crushing and unloading onto means of transport. It is therefore not surprising that these machines are so popular.
The market share of this type of machine is systematically growing, which in turn affects the demand for spare parts, in this case crushers for forage harvesters. Two crushers for the forage harvester are part of the shredding unit, which wears out during operation. The milled teeth, which create a kind of notched surface, are subject to wear, in other words, abrasion. The two crushers of the forage harvester are placed parallel to each other, creating a gap.
The quality of the obtained chaff depends on the gap size setting. Over the years, the form of the notched surface has changed, i.e. from straight teeth to the most efficient directional teeth. Inclined teeth are used less often because, despite numerous tests, we have not achieved satisfactory parameters for the processing of organic matter.
Appropriate parameters of crushers for forage harvesters
Therefore, the crusher of a forage harvester should have appropriate quality and durability parameters to slow down its wear as much as possible and to obtain appropriate parameters and characteristics of the collected organic matter, which in turn determines the receipt of good quality silage for cows and fattening cattle. The quality of the chaff is determined by the average length of the chaff, the degree of fragmentation and the percentage of grains not crushed by the crushers. These parameters are important in cattle breeding because particles that are too short lead to metabolic disorders, and too long particles make it more difficult to ensile.
Crushers for forage harvesters from Skrawit
At Skrawit, crushers for forage harvesters are made of selected material with the addition of chrome. The chromium content in the steel makes the crusher of the forage harvester resistant to abrasion. Tests carried out by farmers show that the crushers for our forage harvesters can withstand approx. 1,000 ha, producing good quality chaff throughout their entire operation period, with uniform tooth abrasion. For three years, we tested various materials from which we obtained the product currently manufactured, proven by forage harvester users, and about which there were no complaints.
Stages of production of crushers
The first stage of production is collecting the material, i.e. ordering it from the steelworks and transporting it to the plant. Then the material is cut into sections of the appropriate length because forage harvester crushers vary in length depending on their type. After preparing the appropriate length of sections, machining takes place, i.e. turning and time-consuming milling of the surface into the form of straight teeth (tooth angle 90o), oblique or directional teeth (tooth angle 60o).
The tests conducted show that the directional teeth are the most efficient in grinding plant matter. Worse results were achieved by crushers for forage harvesters with straight and oblique teeth. After mechanical processing, each crusher of the forage harvester is subjected to dedicated heat treatment processes. You should pay attention to obtaining the appropriate hardness because if it is low, the crushers for forage harvesters will wear out quickly, if it is high, they will crumble.
This is followed by further mechanical processing, roll finishing, and balancing. For this purpose, the CMT-300 H2P balancing machine is used, which undergoes an annual service inspection to obtain accurate measurement results. Each crusher of the forage harvester is drilled during balancing, if necessary until good parameters are obtained. Previously, we achieved the right balance by welding weights, but the aesthetics suffered greatly.